Motor Driver
This product is a Driver for Ultrasonic Motors (drive circuit).
User can select the driver in some lineup, low cost simple model, the model that has speed control function by encoder signals, the model that has voltage boost function to improve the start movement.
D6030/24V : Driver for Ultrasonic Motor USR30 Series
D6030/24V
-
D6030 is the driver for Ultrasonic Motor USR30 Series.
By adopting D6030, customers can build the low cost control system for USR30 series.
By using TTL level signal(0[V], 5[V]), D6030 can change the direction of rotation(CW, CCW, Stop).
By using Analog voltage:DC 0[V] 〜 3.2[V], D6030 can change the speed of the Ultrasonic Motor USR30 Series.Click here for catalog and manuals
Click here for Drawing and CAD data
Contact Products from here
Specification
Power Source Voltage | DC24 [V] ±0.5 [V] |
Oscillation Waveform | Pseudo Sine Wave |
Oscillation Frequency | 49 [KHz]〜55 [KHz] |
Speed Adjustment Method | Frequency Modulation Method |
Frequency Control | Automatic Tracking Method Using Feedback of Amplitude by Vibration |
Motor Drive Voltage | 110 [Vrms] |
Consumption Current | DC24V : 0.8 [A] / DC12V : 1.5[A] |
Over Current Protection | 24V : 0.8 [A] (φ5.2 Midget Fuse) 12V : 1.5[A](φ5.2 Midget Fuse) |
Insulation Resistance | Over 10 [MΩ] (Motor Unconnected) |
Withstand Voltage | 1 [KVAC] (Motor Unconnected) |
Storage Temperature | -20 [℃] 〜 +80 [℃] |
Working Temperature | -10 [℃] 〜 +55 [℃] |
Start-Stop Control | Switing TTL Level Voltage |
Starting Response | Less than 50 [ms] (with no load) |
Stopping Response | Less than 1 [ms] (with no load) |
No-load Adjustable Speed Range | 30 [rpm] 〜 300 [rpm] |
Speed Setting External Voltage | DC 0 [V] 〜 3.2 [V] |
Recommended Switch | Toggle Switch(ON-OFF-ON) |
Recommended Volume | 10 [KΩ], 0.1 [W], B type |
Weight | 105 [g] |
Outline Size | Vertical x Horizontal x Height:56 [mm]×71 [mm]×22 [mm] |
Remarks | 12V specifications are available upon consultation. |
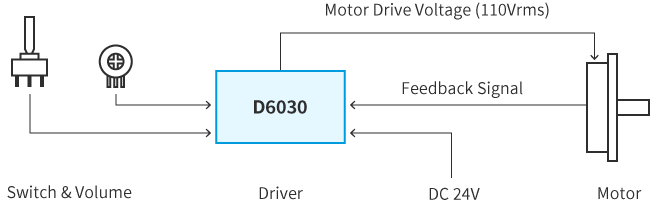
By connecting an external switch to D6030, the action of a motor can be operated.
(Rotative-direction change of CW-CCW, and a Stop of the Ultrasonic Motor) and Speed can be changed by connecting volume.
In order to stabilize the speed of a motor, it is necessary to input a feedback signal into D6030.
*If a Ultrasonic Motor generates heat, the speed of a motor may become slow.
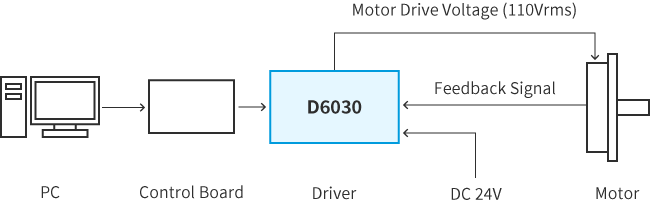
In order to control a Ultrasonic Motor, signals are sent to D6030 from a control board.
For the rotative-direction change of CW-CCW, and a Stop of the Ultrasonic Motor, two signals of a TTL level are required.
For speed change, the analog signal of DC 0 [V] – 3.2 [V] is required.
In order to stabilize the speed of a motor, it is necessary to input a feedback signal into D6030.
*If a Ultrasonic Motor generates heat, the speed of a motor may become slow.
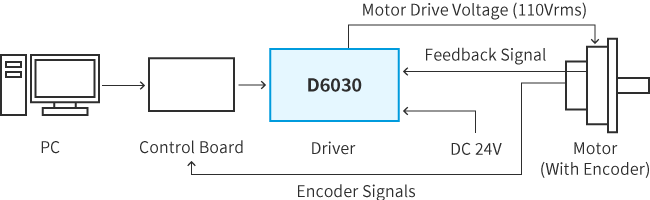
In order to control a Ultrasonic Motor, signals are sent to D6030 from a control board.
For the rotative-direction change of CW-CCW, and a Stop of the Ultrasonic Motor, two signals of a TTL level are required.
For speed change, the analog signal of DC 0 [V] – 3.2 [V] is required.
In order to stabilize the speed of a motor, it is necessary to input a feedback signal into D6030.
By using the encoder signals of a motor by an external control board, the speed and the position of a motor is controllable.
*If the control Board does not control the speed of a motor, there is a possibility that the speed of a motor may become slow by the heat of motor.
D6060/24V : Driver for Ultrasonic Motor USR60 Series
D6060/24V
-
D6060 is the driver for Ultrasonic Motor USR60 Series.
By adopting D6060, customers can build the low cost control system for USR60 series.
By using TTL level signal(0[V], 5[V]), D6060 can change the direction of rotation(CW, CCW, Stop).
By using Analog voltage:DC 0[V] 〜 3.2[V], D6060 can change the speed of the Ultrasonic Motor USR60 Series.Click here for catalog and manuals
Click here for Drawing and CAD data
Contact Products from here
Specification
Power Source Voltage | DC24 [V] ±0.5 [V] |
Oscillation Waveform | Pseudo Sine Wave |
Oscillation Frequency | 40 [KHz]〜45 [KHz] |
Speed Adjustment Method | Frequency Modulation Method |
Frequency Control | Automatic Tracking Method Using Feedback of Amplitude by Vibration |
Motor Drive Voltage | 130 [Vrms] |
Consumption Current | DC24V : 2.0 [A] / DC12V : 4.0[A] |
Over Current Protection | 24V : 2.5 [A] (φ5.2 Midget Fuse) 12V : 4[A](φ5.2 Midget Fuse) |
Insulation Resistance | Over 10 [MΩ] (Motor Unconnected) |
Withstand Voltage | 1 [KVAC] (Motor Unconnected) |
Storage Temperature | -20 [℃] 〜 +80 [℃] |
Working Temperature | -10 [℃] 〜 +55 [℃] |
Start-Stop Control | Switing TTL Level Voltage |
Starting Response | Less than 50 [ms] (with no load) |
Stopping Response | Less than 1 [ms] (with no load) |
No-load Adjustable Speed Range | 15 [rpm] 〜 130 [rpm] |
Speed Setting External Voltage | DC 0 [V] 〜 3.2 [V] |
Recommended Switch | Toggle Switch(ON-OFF-ON) |
Recommended Volume | 10 [KΩ], 0.1 [W], B type |
Weight | 250 [g] |
Outline Size | Vertical x Horizontal x Height:83 [mm]×100 [mm]×35 [mm] |
Remarks | 12V specifications are available upon consultation. |
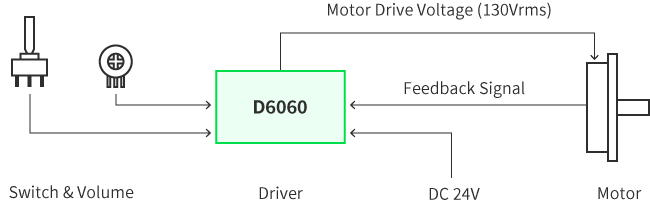
By connecting an external switch to D6060, the action of a motor can be operated.
(Rotative-direction change of CW-CCW, and a Stop of the Ultrasonic Motor)
And Speed can be changed by connecting volume.
In order to stabilize the speed of a motor, it is necessary to input a feedback signal into D6060.
*If a Ultrasonic Motor generates heat, the speed of a motor may become slow.
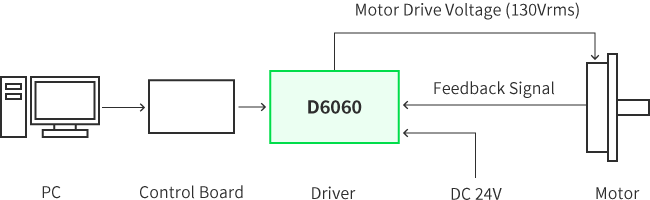
In order to control a Ultrasonic Motor, signals are sent to D6060 from a control board.
For the rotative-direction change of CW-CCW, and a Stop of the Ultrasonic Motor, two signals of a TTL level are required.
For speed change, the analog signal of DC 0 [V] – 3.2 [V] is required.
In order to stabilize the speed of a motor, it is necessary to input a feedback signal into D6060.
*If a Ultrasonic Motor generates heat, the speed of a motor may become slow.
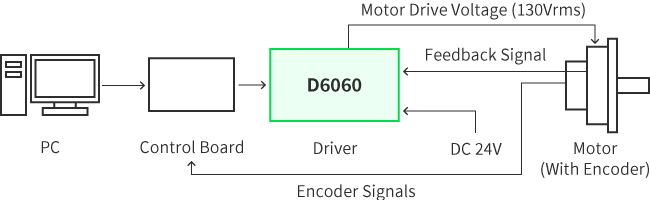
In order to control a Ultrasonic Motor, signals are sent to D6060 from a control board.
For the rotative-direction change of CW-CCW, and a Stop of the Ultrasonic Motor, two signals of a TTL level are required.
For speed change, the analog signal of DC 0 [V] – 3.2 [V] is required.
In order to stabilize the speed of a motor, it is necessary to input a feedback signal into D6060.
By using the encoder signals of a motor by an external control board, the speed and the position of a motor is controllable.
*If the control Board does not control the speed of a motor, there is a possibility that the speed of a motor may become slow by the heat of motor.
D6060E/24V : Driver for Ultrasonic Motor USR30 and USR60 Series
D6060E/24V
-
D6060E is the driver for Ultrasonic Motor USR30, USR60 Series.
D6060E has the function of Auto Speed Control by the encoder signals.
By adopting D6060E, customers can build the system which stabilized the speed of the Ultrasonic Motor USR30, USR60 Series.
By using TTL level signal(0[V], 5[V]), D6060E can change the direction of rotation(CW, CCW, Stop).
By using Analog voltage:DC 0[V] 〜 3.2[V], D6060E can change the speed of the Ultrasonic Motor USR30, USR60 Series.Click here for catalog and manuals
Click here for Drawing and CAD data
Contact Products from here
Specification
Power Source Voltage | DC24 [V] ±0.5 [V] |
Oscillation Waveform | Pseudo Sine Wave |
Oscillation Frequency | 40 [KHz]〜45 [KHz] |
Speed Adjustment Method | Frequency Modulation Method |
Frequency Control | Automatic Tracking Method Using Feedback of Amplitude by Vibration |
Motor Drive Voltage | 130 [Vrms] |
Consumption Current | DC24V : 2.0 [A] / DC12V : 4.0[A] |
Over Current Protection | 24V : 2.5 [A] (φ5.2 Midget Fuse) 12V : 4[A](φ5.2 Midget Fuse) |
Insulation Resistance | Over 10 [MΩ] (Motor Unconnected) |
Withstand Voltage | 1 [KVAC] (Motor Unconnected) |
Storage Temperature | -20 [℃] 〜 +80 [℃] |
Working Temperature | -10 [℃] 〜 +55 [℃] |
Start-Stop Control | Switing TTL Level Voltage |
Starting Response | Less than 50 [ms] (with no load) |
Stopping Response | Less than 1 [ms] (with no load) |
No-load Adjustable Speed Range | 15 [rpm] 〜 150 [rpm] |
Speed Setting External Voltage | DC 0 [V] 〜 3.2 [V] |
Recommended Switch | Toggle Switch(ON-OFF-ON) |
Recommended Volume | 10 [KΩ], 0.1 [W], B type |
Weight | 260 [g] |
Outline Size | Vertical x Horizontal x Height:83 [mm]×100 [mm]×35 [mm] |
Remarks | Speed Control Function using an Encoder Signal is equipped. 12V specifications are available upon consultation. |
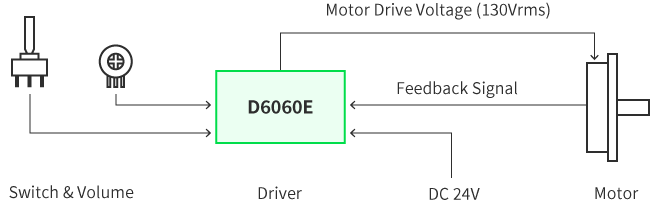
By connecting an external switch to D6060E, the action of a motor can be operated.
(Rotative-direction change of CW-CCW, and a Stop of the Ultrasonic Motor) And Speed can be changed by connecting volume.
In order to stabilize the speed of a motor, it is necessary to input a feedback signal into D6060E.
*If a Ultrasonic Motor generates heat, the speed of a motor may become slow.
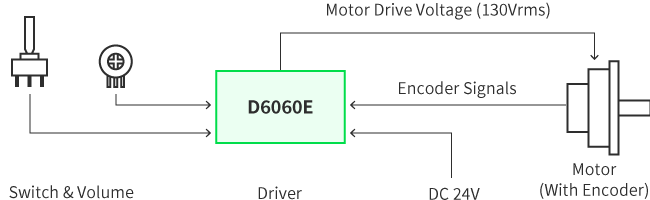
By connecting an external switch to D6060E, the action of a motor can be operated.
(Rotative-direction change of CW-CCW, and a Stop of the Ultrasonic Motor) And Speed can be changed by connecting volume.
D6060E uses the encoder signals from a motor, and stabilizes the speed of a motor.
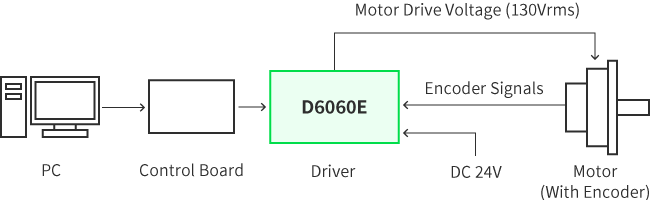
In order to control a Ultrasonic Motor, signals are sent to D6060E from a control board.
For the rotative-direction change of CW-CCW, and a Stop of the Ultrasonic Motor, two signals of a TTL level are required.
For speed change, the analog signal of DC 0 [V] – 3.2 [V] is required.
D6060E uses the encoder signals from a motor, and stabilizes the speed of a motor.
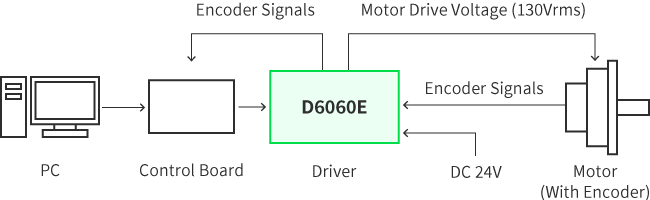
In order to control a Ultrasonic Motor, signals are sent to D6060E from a control board.
For the rotative-direction change of CW-CCW, and a Stop of the Ultrasonic Motor, two signals of a TTL level are required.
For speed change, the analog signal of DC 0 [V] – 3.2 [V] is required.
D6060E uses the encoder signals from a motor, and stabilizes the speed of a motor.
By using the encoder signals of a motor by an external control board, the speed and the position of a motor is controllable.
D6060S/24V : Driver for Ultrasonic Motor USR30 and USR60 Series
D6060S/24V
-
D6060S is the driver for Ultrasonic Motor USR30, USR60 Series.
D6060S has the function of Auto Speed Control by the encoder signals.
And D6060S has the release function of slight sticking of the Motor.
By adopting D6060S, customers can improve the stability of the whole Ultrasonic Motor System.
By using TTL level signal(0[V], 5[V]), D6060E can change the direction of rotation(CW, CCW, Stop).
By using Analog voltage:DC 0[V] 〜 3.2[V], D6060E can change the speed of the Ultrasonic Motor USR30, USR60 Series.Click here for catalog and manuals
Click here for Drawing and CAD data
Contact Products from here
Specification
Power Source Voltage | DC24 [V] ±0.5 [V] |
Oscillation Waveform | Pseudo Sine Wave |
Oscillation Frequency | 40 [KHz]〜45 [KHz] |
Speed Adjustment Method | Frequency Modulation Method |
Frequency Control | Automatic Tracking Method Using Feedback of Amplitude by Vibration |
Motor Drive Voltage | 130 [Vrms] |
Consumption Current | Maximum 2.0 [A] |
Over Current Protection | 2.5 [A] (φ5.2 Midget Fuse) |
Insulation Resistance | Over 10 [MΩ] (Motor Unconnected) |
Withstand Voltage | 1 [KVAC] (Motor Unconnected) |
Storage Temperature | -20 [℃] 〜 +80 [℃] |
Working Temperature | -10 [℃] 〜 +55 [℃] |
Start-Stop Control | Switing TTL Level Voltage |
Starting Response | Less than 50 [ms] (with no load) |
Stopping Response | Less than 1 [ms] (with no load) |
No-load Adjustable Speed Range | 15 [rpm] 〜 150 [rpm] |
Speed Setting External Voltage | DC 0 [V] 〜 3.2 [V] |
Recommended Switch | Toggle Switch(ON-OFF-ON) |
Recommended Volume | 10 [KΩ], 0.1 [W], B type |
Weight | 280 [g] |
Outline Size | Vertical x Horizontal x Height:83 [mm]×100 [mm]×35 [mm] |
Remarks | Speed Control Function using an Encoder Signal is equipped. The release function of slight sticking by the boost circuit of the starting characteristic is equipped. |
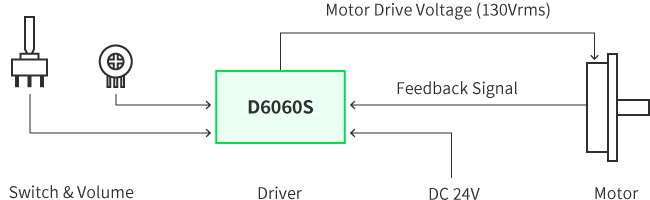
By connecting an external switch to D6060S, the action of a motor can be operated.
(Rotative-direction change of CW-CCW, and a Stop of the Ultrasonic Motor)
And Speed can be changed by connecting volume.
In order to stabilize the speed of a motor, it is necessary to input a feedback signal into D6060S.
*If a Ultrasonic Motor generates heat, the speed of a motor may become slow.
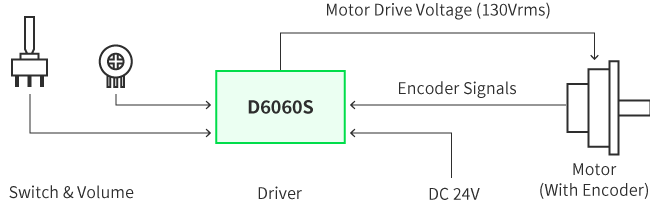
By connecting an external switch to D6060S, the action of a motor can be operated.
(Rotative-direction change of CW-CCW, and a Stop of the Ultrasonic Motor)
And Speed can be changed by connecting volume.
D6060S uses the encoder signals from a motor, and stabilizes the speed of a motor.
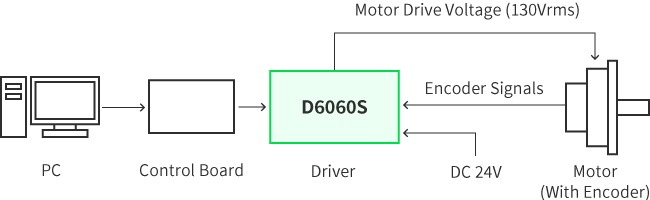
In order to control a Ultrasonic Motor, signals are sent to D6060S from a control board.
For the rotative-direction change of CW-CCW, and a Stop of the Ultrasonic Motor, two signals of a TTL level are required.
For speed change, the analog signal of DC 0 [V] – 3.2 [V] is required.
D6060S uses the encoder signals from a motor, and stabilizes the speed of a motor.
ON-OFF of the release function of slight sticking is changed from a control board by inputting the signal of a TTL level.

In order to control a Ultrasonic Motor, signals are sent to D6060S from a control board.
For the rotative-direction change of CW-CCW, and a Stop of the Ultrasonic Motor, two signals of a TTL level are required.
For speed change, the analog signal of DC 0 [V] – 3.2 [V] is required.
D6060S uses the encoder signals from a motor, and stabilizes the speed of a motor.
ON-OFF of the release function of slight sticking is changed from a control board by inputting the signal of a TTL level.
By using the encoder signals of a motor by an external control board, the speed and the position of a motor is controllable.
Other models